In store and store management, maintenance costs can represent a significant portion of the operating budget. Optimizing these expenses is essential to improve profitability and ensure efficiency in daily operations.
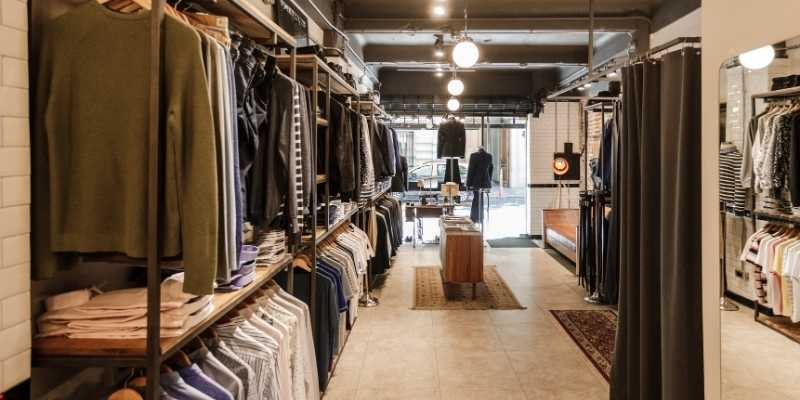
Reducing maintenance costs is not only about reducing the amount of money spent, but also about implementing strategies that allow you to get the most out of every available resource. From digitization to the correct distribution of tasks, every step counts to transform the maintenance processes in the store.
How the right distribution of tasks improves efficiency
Efficiency in stores depends on the correct distribution of maintenance tasks among staff. As experienced in several business environments, a disorganized distribution not only leads to delays, but also leads to an underutilization of talent and available resources. The key is to assign tasks according to the availability and skills of each technician.
A clear example of this is seen in the personal experience of the store where a new work assignment methodology was implemented. This consisted of evaluating the workload of each technician and assigning tasks according to their availability and specialization. Not only did this improve productivity, but it also reduced downtime, ensuring technicians were constantly busy with jobs that matched their capabilities.
Minimizing waiting times: keys to an efficient workflow
One of the main factors that affect the efficiency of a store is the time wasted waiting for job approvals or parts to arrive. These delays can lead to a chain of inefficiencies, where technicians lose valuable time while waiting for these obstacles to be resolved. Implementing a system that minimizes these wait times is crucial to improving profitability.
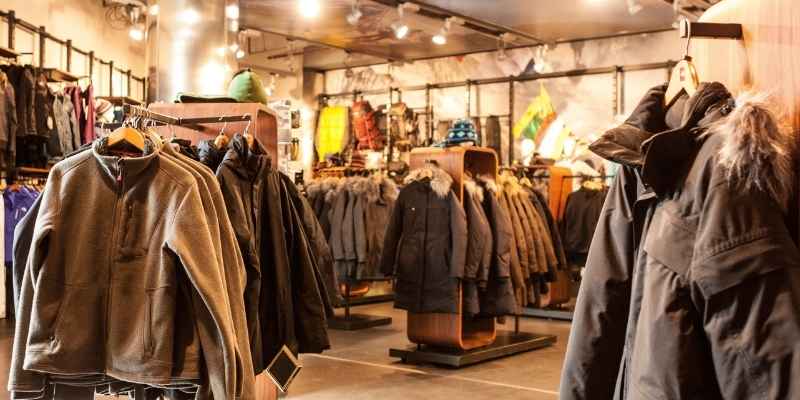
In the case of the aforementioned store, advance planning was adopted to ensure that technicians had all the necessary parts before starting a job. In addition, the approval of works was done immediately, avoiding that technicians had to wait while other jobs were resolved. By integrating these practices, the store was able to maintain a steady flow of work without interruptions, which led to a significant increase in overall efficiency.
The Impact of Advance Planning on Reducing Operating Costs
Planning ahead is one of the most powerful strategies for reducing operating costs in any work environment. Lack of planning not only causes chaos, but also leads to inefficient use of resources. In the store in question, an early diagnosis system was implemented that allowed parts and resource needs to be identified before problems arose.
By planning ahead, technicians were prevented from having to wait for parts or tasks from being delayed due to lack of preparation. This planning made it possible to optimize repair times, which in turn reduced operating costs by avoiding downtime and improving the use of available resources.
How to choose the right technology to manage maintenance
Technology plays a crucial role in optimizing in-store maintenance processes. Digital management tools allow for more precise control of operations, efficient maintenance scheduling, and detailed tracking of resource and parts usage. Choosing the right platforms, such as computerized maintenance management systems (CMMS), helps improve coordination and reduce the chance of errors.
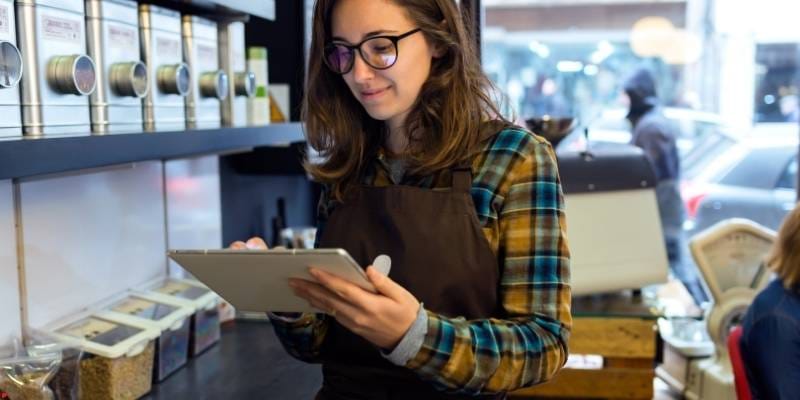
Implementing technology not only improves accuracy, but also helps reduce costs in the long run. These platforms allow you to track the status of equipment in real time, forecast future needs, and manage parts inventories more effectively.
Avoid costly errors with proper parts and spare parts management
A key aspect of reducing maintenance costs is the effective management of parts and spare parts. Common mistakes, such as ordering incorrect parts or not anticipating needs in advance, can result in costly delays. At the aforementioned store, a more rigorous inventory management system was adopted that ensured that the right parts were available before any work began.
In addition, staff were trained to identify exact part needs using VIN codes and other specific diagnostic tools. This avoided costly errors arising from incorrect orders, significantly reducing downtime and additional costs.
The importance of ongoing training for maintenance personnel
Continuous training of maintenance personnel is essential to maintain efficiency and reduce operating costs. Well-trained technicians not only complete jobs faster, but they are also less likely to make mistakes, reducing costs related to incorrect or poorly managed repairs. The aforementioned store constantly invests in the training of its technicians, ensuring that they are up to date with the latest technologies and maintenance practices.
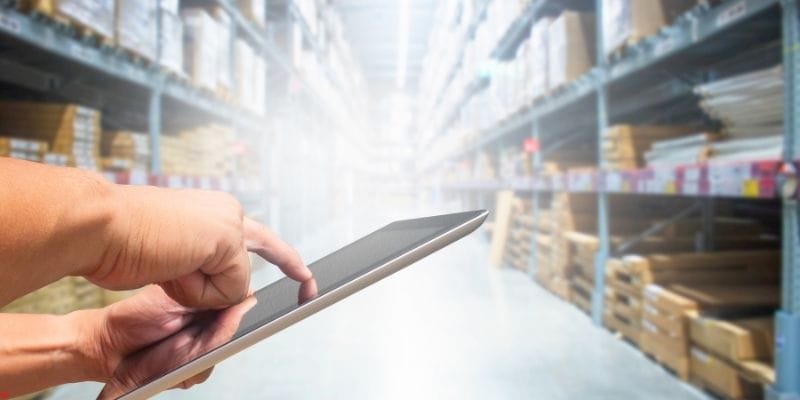
In addition, training allows technicians to be more autonomous, reducing the need for constant supervision and increasing the speed with which jobs can be completed.
Benefits of digitalization in store maintenance management
Digitalization has revolutionized many aspects of maintenance management, allowing for greater accuracy in task tracking, scheduling, and inventory management. In the aforementioned store, the adoption of digital platforms made it possible to automate many of the manual processes, such as task assignment and inventory management, which reduced human errors and improved overall efficiency.
Digitization also allows for better data analysis, making it easier to identify areas for improvement and make informed decisions about how to allocate resources more efficiently.
Case Study: How One Store Optimized Its Maintenance Costs by 30%
A success story in reducing maintenance costs was experienced in a store that managed to reduce its operating expenses by 30% by implementing efficiency strategies. By adopting advance planning, distributing tasks correctly, and ensuring they had the right parts available, the store was able to maximize their productivity without incurring additional expenses. This integrated approach helped improve profitability and customer satisfaction, while optimizing the use of resources.
Conclusions and best practices to reduce maintenance costs
Reducing maintenance costs in stores is a task that requires strategy, organization and the correct implementation of technological tools. Through advance planning, correct task distribution, continuous training, and the use of technology, stores can significantly reduce their operating expenses and improve maintenance efficiency. Applying these best practices not only leads to cost reduction, but also improves service quality and customer satisfaction.