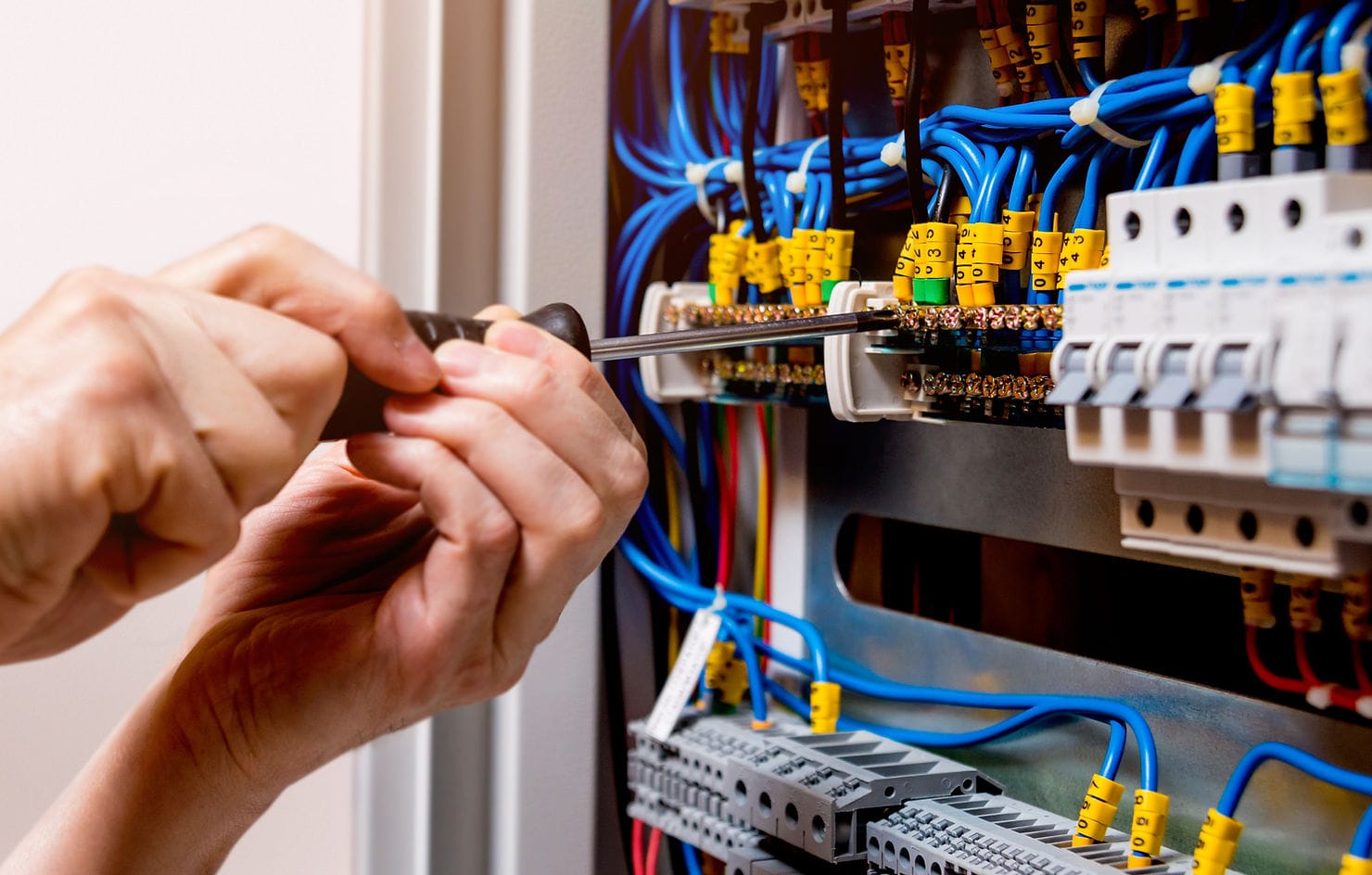
Implementing progressive preventive maintenance extends the lifespan of your commercial equipment and infrastructure, among other benefits. If you want to learn about these benefits, we invite you to keep reading, as we will explain them in detail later on.
Many facility management teams choose to operate under a “if it’s not broken, don’t fix it” management style, but relying solely on reactive maintenance leaves your retail store vulnerable to additional costs, potential extended downtime, and loss of productivity.
Urgent reactive maintenance must consider the cost of urgently sourcing necessary machine parts, compensating qualified technicians, and the potential interruption of sales revenue or productive capacity while the equipment is out of service.
Worse still, not properly implementing preventive maintenance could result in the need for complete equipment replacement, leading to a steep increase in costs.
The initial costs of performing preventive maintenance might seem intimidating at first, especially if your facility operates on a tight budget. However, maintaining your equipment is an investment in the future of your retail store.
At Optima Retail, we excel in offering comprehensive retail maintenance services, ensuring facilities remain in impeccable condition to meet our clients’ demands.
7 Reasons Why Preventive Maintenance is Essential for Retail Sector Success
Regularly scheduled maintenance tasks are crucial for the success of the retail sector. Below, we list 7 benefits of implementing preventive maintenance that every facility leader and retail business owner should know:
1. Extend Asset Lifespan
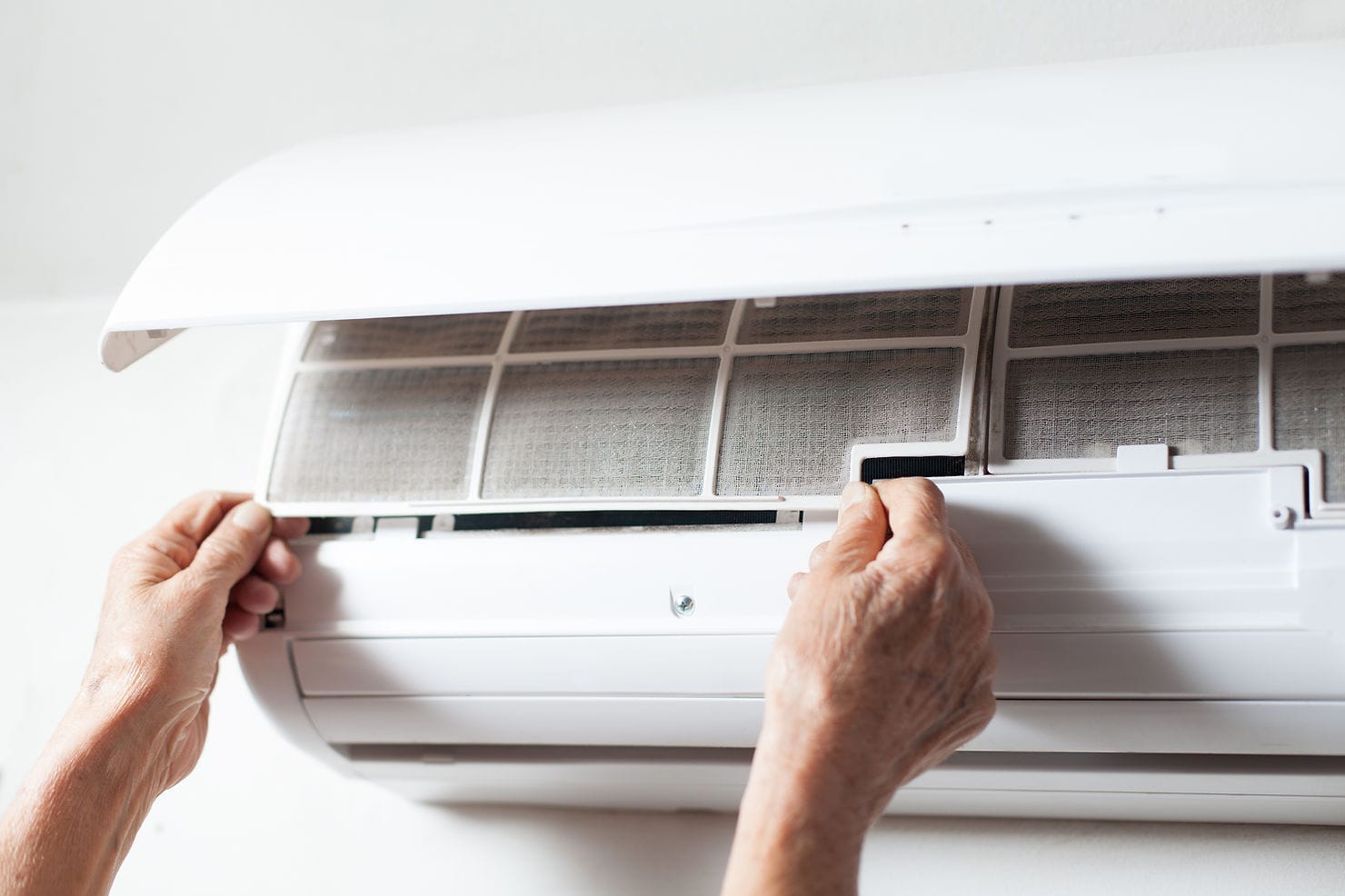
Arguably the most important benefit of preventive maintenance is an extended asset lifespan. Keeping your equipment in good condition allows it to operate for longer periods, reducing maintenance costs and preventing losses due to downtime.
Information tracking systems enable you to plan preventive maintenance at the right time, detecting potential equipment issues before a breakdown occurs.
The power of a good downtime tracking system is so impactful that 78% of companies implementing preventive maintenance report increased equipment durability.
2. Lower Risk of Breakdowns
Waiting until equipment fails to perform maintenance puts your facility at risk of productivity loss and affects your reputation.
Only around 10% or less of retail sector equipment actually wears out due to proper use; this means that 90% of mechanical failures stem from preventable problems, which can be avoided with a well-implemented preventive maintenance plan.
By proactively scheduling maintenance, you can significantly reduce the risk of equipment failures in your retail store, providing you with greater peace of mind as a facility owner.
3. Increase Efficiency
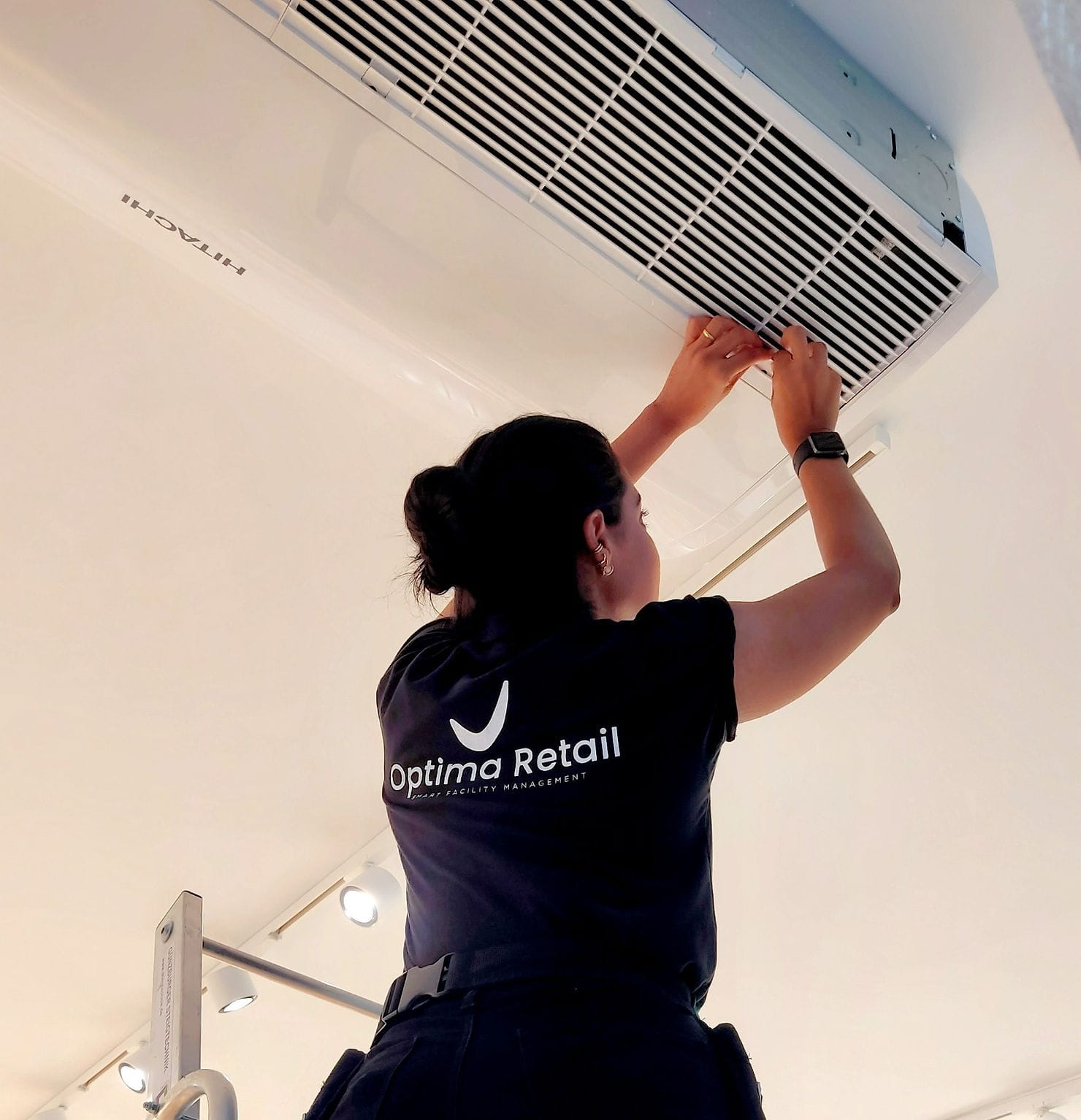
In addition to a longer lifespan, equipment that receives routine preventive maintenance also operates more efficiently. Overall Equipment Effectiveness (OEE) is a common maintenance management KPI that measures efficiency.
OEE categorizes equipment into three areas. Equipment such as HVAC units see improvements in all aspects as a result of preventive maintenance:
- Availability: Downtime for reactive maintenance is usually longer than for scheduled preventive maintenance, so choosing preventive maintenance means more uptime and equipment availability.
- Performance: Properly maintained HVAC units can better maintain air at a set temperature and distribute it evenly throughout the space.
- Quality: A regularly cleaned HVAC unit’s air filter and coils will heat and cool more effectively, producing cleaner and higher-quality air.
4. Reduce Unplanned Downtime
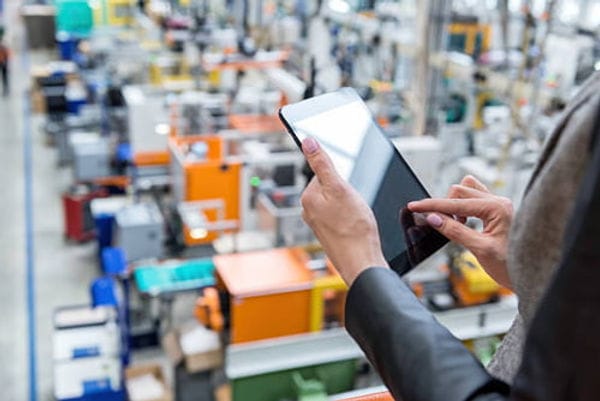
Whether you choose to rely on preventive or reactive maintenance, machine downtime is inevitable during maintenance. However, downtime can be significantly reduced by scheduling maintenance in advance with a preventive maintenance plan.
In the case of a reactive maintenance repair, machine downtime can be prolonged due to waiting times for specialized mechanics or the shipping time for necessary parts.
With preventive maintenance, you have the opportunity to schedule the procedure at a convenient time for you and your facility (i.e., when occupants are out of the building or operations have concluded for the day), minimizing interruptions to production and efficiency.
5. Promote Health and Safety
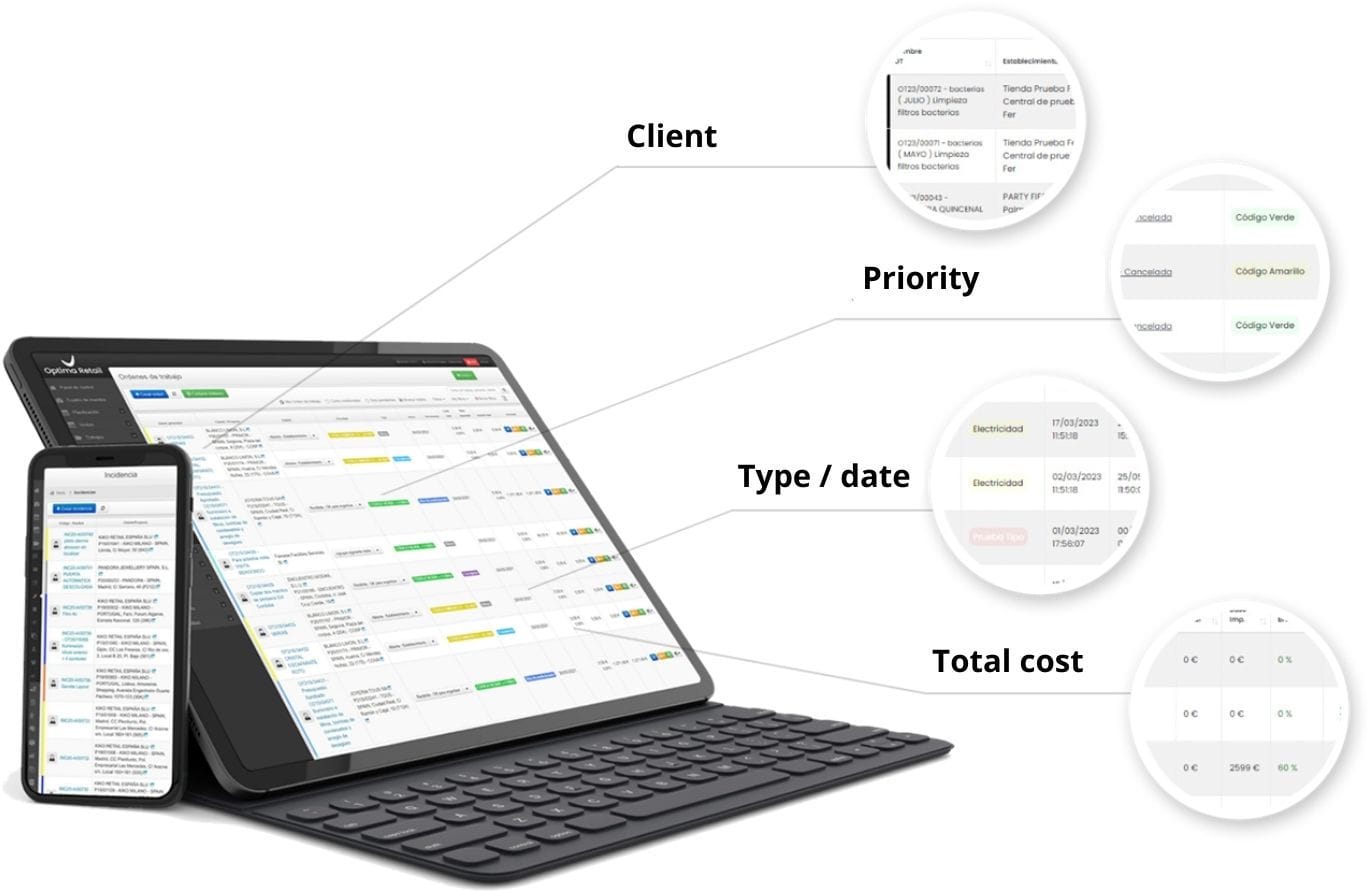
In the context of preventive maintenance, health, and safety are often a major concern in facilities with hazardous equipment. However, health and safety are important in all facilities, including retail buildings.
Tracking preventive maintenance with a Computerized Maintenance Management System (CMMS) allows you to monitor all equipment in your facility and store essential safety information in a digital hub.
Using CMMS software also simplifies safety audits: with a few clicks on a smartphone, the complete maintenance history and safety protocols for all equipment elements will be available. Preventive maintenance and CMMS software can help your facility prepare for fire safety.
6. Increase Customer Satisfaction
Ensuring that equipment always operates as efficiently as possible translates directly into cost savings and increased revenue. It also helps build a strong brand image and boosts customer satisfaction.
7. Save Money
All the reasons listed above lead to a final benefit of preventive maintenance: cost savings. Unplanned maintenance typically costs 3 to 9 times more than planned maintenance.
Find unbeatable deals at Optima Retail! Get your personalized quote today. Quality and savings are here. Don’t miss out!